The Power of Mold Injection Plastic in Modern Manufacturing
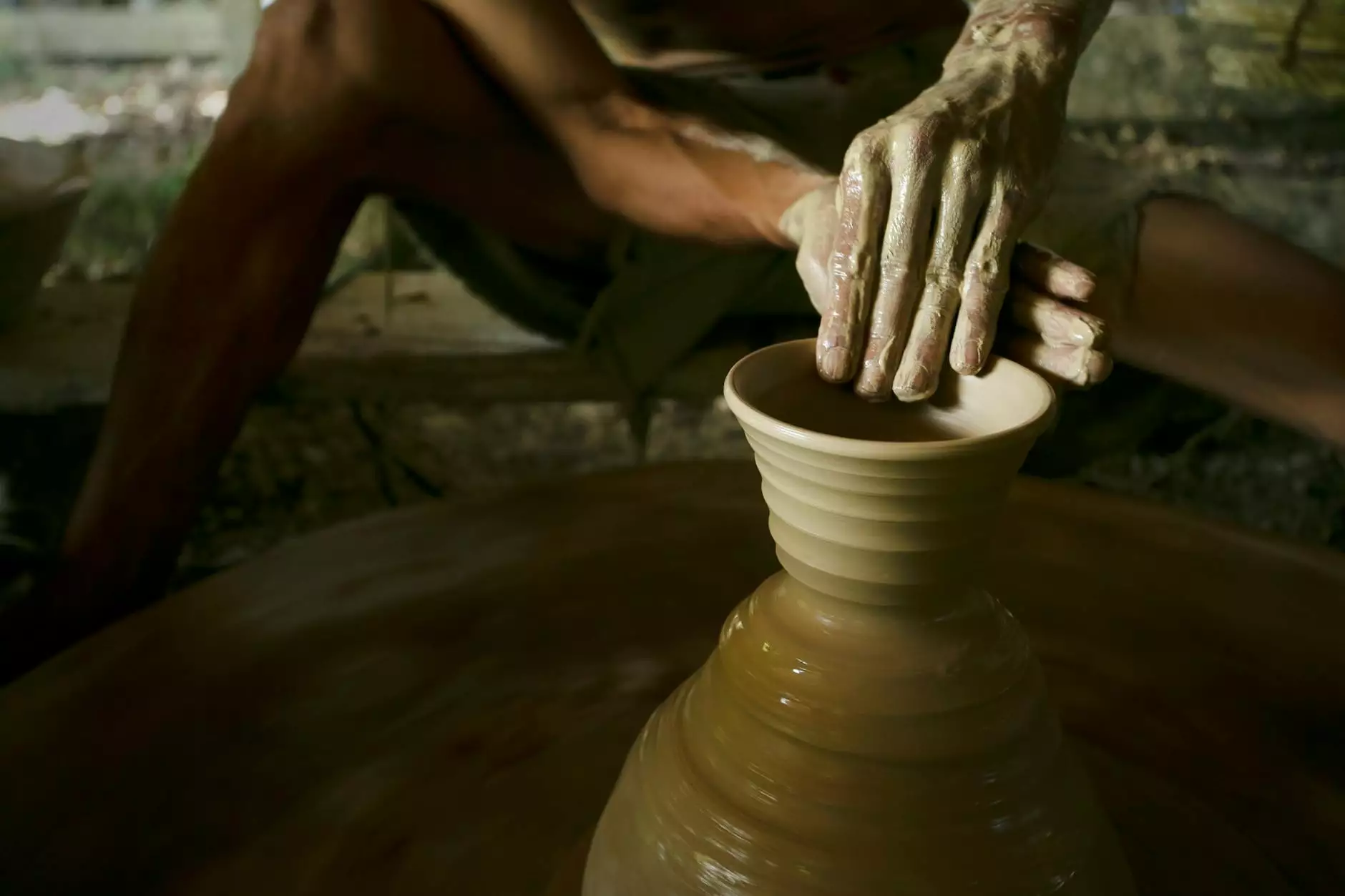
Mold injection plastic is a revolutionary process in the realm of manufacturing, with significant implications across various industries. This technique not only streamlines production but also enhances the quality and precision of the end products. In this article, we will explore the intricate details of mold injection plastic, its applications, advantages, and why it stands out for businesses, particularly in the field of metal fabricators.
Understanding Mold Injection Plastic
Mold injection plastic is a manufacturing technique that involves the injection of molten plastic into a mold cavity, which then solidifies to form the desired product. This method has gained immense popularity due to its efficiency and scalability in production.
The Injection Molding Process
The injection molding process can be broken down into several critical steps:
- Material Selection: The type of plastic to be used is chosen based on the required properties of the final product.
- Mold Design: A mold is designed and manufactured, tailored to the specific part that needs to be produced.
- Injection: The plastic is heated until it becomes molten and then injected into the mold.
- Cooling: The mold is allowed to cool, solidifying the plastic into the desired shape.
- Demolding: The finished product is removed from the mold.
Advantages of Mold Injection Plastic
The benefits of utilizing mold injection plastic are numerous and significant:
1. High Efficiency and Production Rates
One of the primary advantages is the high efficiency associated with this manufacturing process. Once the mold is designed, a large number of parts can be produced in a relatively short timeframe, making it ideal for high-volume production.
2. Consistency and Precision
With the automation of the injection molding process, it ensures that each part produced is consistent in size and quality. This precision is crucial for components where minor deviations can lead to significant performance issues.
3. Design Flexibility
The flexibility offered by mold injection plastic molding allows designers to create complex shapes and intricate features, something that is often challenging with other manufacturing processes. This capability to innovate can lead to products that outperform competitors.
4. Material Variety
A plethora of plastic materials can be used in injection molding, each offering varying properties like strength, flexibility, and heat resistance. This allows manufacturers to choose materials that best fit their product's requirements.
5. Cost-Effectiveness
Although the initial cost for mold design and creation can be high, the long-term cost savings due to mass production and reduced wastage make mold injection plastic a highly cost-effective choice.
Applications of Mold Injection Plastic
Mold injection plastic finds applications in numerous sectors, especially in the manufacturing domain.
1. Automotive Industry
From dashboard components to interior fixtures, injection-molded plastics play a crucial role in the automotive industry by providing lightweight, durable parts that can enhance fuel efficiency and reduce vehicle weight.
2. Electronics
The electronics sector benefits from mold injection plastic through the creation of high-precision components, enclosures, and fittings that are essential for the protection and functionality of electronic devices.
3. Healthcare
Medical devices often require high standards of hygiene and accuracy, making mold injection plastic an ideal choice for producing components that meet strict regulatory requirements.
4. Consumer Goods
Everyday items such as toys, kitchen appliances, and furniture components are often produced using mold injection, demonstrating its versatility and wide-ranging applications.
Mold Injection Plastic in Metal Fabrication
The Role of Metal Fabricators
Metal fabricators like DeepMould.net are beginning to integrate mold injection plastic techniques into their operations to diversify their product offerings and enhance the capabilities of their clients. By combining metal parts with plastic components, manufacturers can produce hybrid products that leverage the best of both worlds.
Advantages for Metal Fabricators
- Enhanced Product Durability: Combining metal with molded plastic can yield components that resist wear and improve longevity.
- Cost Reduction: Utilizing light-weight plastic along with metals can reduce shipping and handling costs due to decreased weight.
- Increased Design Options: Fabricators can now explore innovative designs that were previously unattainable using only metal.
The Future of Mold Injection Plastic
The future of mold injection plastic looks bright, with continuous advancements in technology and materials. Integration with industry 4.0 technologies such as automation, AI, and smart manufacturing processes will enhance the efficiency and capabilities of this technique. Emerging trends that are shaping the future of mold injection include:
1. Sustainable Manufacturing
As businesses become more aware of their environmental footprint, the demand for sustainable materials and processes is increasing. The development of biodegradable plastics and recyclable materials for injection molding is paving the way for eco-friendly manufacturing solutions.
2. Customization and On-Demand Production
The rise of customization in consumer products has led to an increased demand for on-demand production capabilities, where mold injection plastic can quickly produce tailored components without extensive lead times.
3. Technological Advancements
Innovations in mold-making technology and materials continue to evolve, leading to faster prototyping and efficient production cycles that can respond swiftly to market needs.
Conclusion
As the manufacturing landscape continues to evolve, mold injection plastic stands out as a quintessential technique that offers unparalleled benefits in precision, efficiency, and versatility. Metal fabricators like DeepMould.net can harness the combined strength of metals and plastics to deliver innovative solutions tailored to the needs of various industries. Investing in and implementing mold injection plastic technology is not just a trend but a strategic move towards enhancing product offerings and ensuring competitive advantage in the market.
In conclusion, understanding and embracing the power of mold injection plastic will not only enhance operational capabilities but will also position businesses to thrive in a fast-paced, increasingly demanding marketplace. Whether you are a seasoned fabricator or a newcomer to the industry, the potential of this technology is waiting to be harnessed.