CNC Lathe Factory: The Backbone of Precision Metal Fabrication
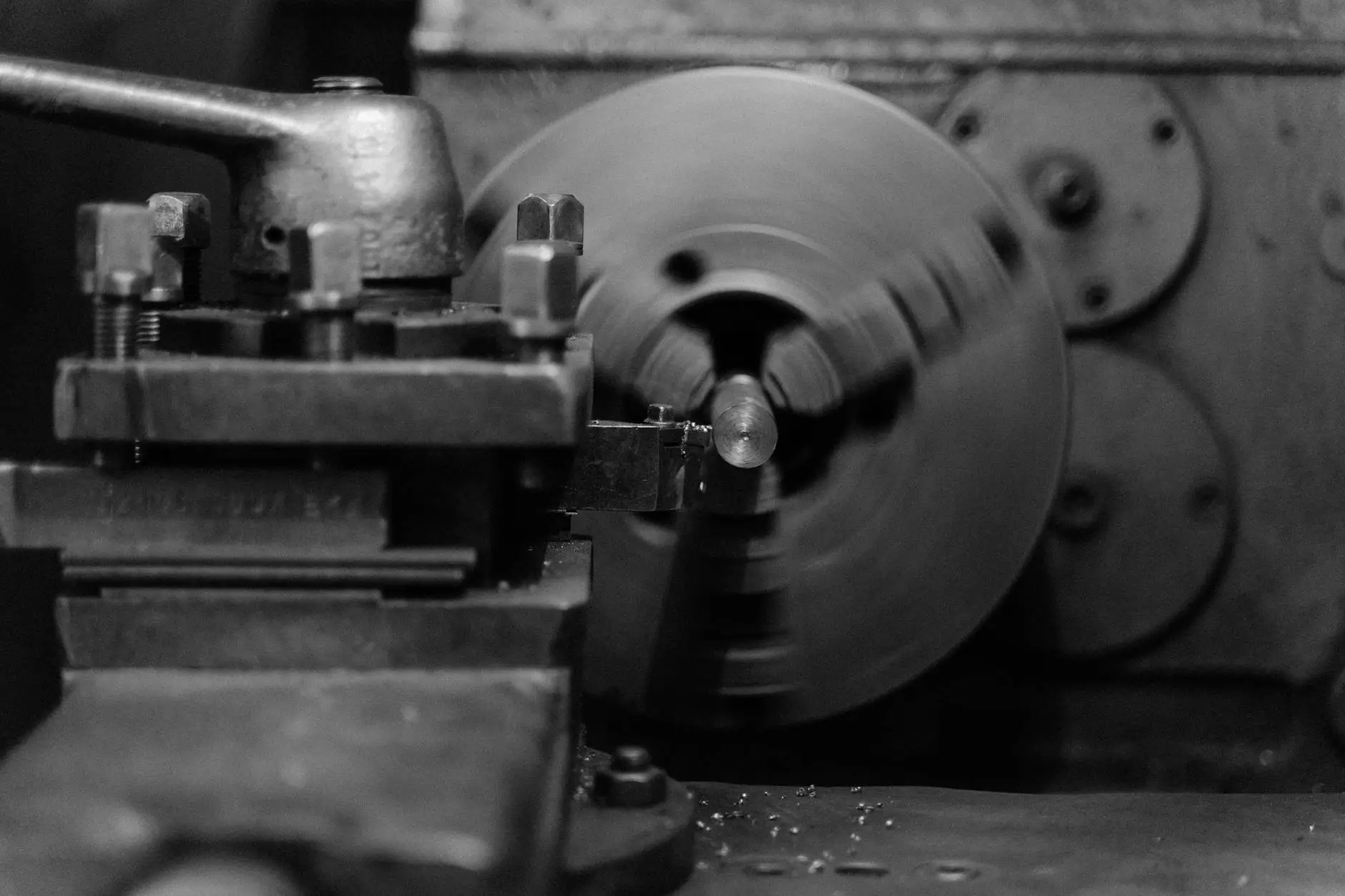
In today's manufacturing landscape, few technologies have made as significant an impact as CNC (Computer Numerical Control) machining. At the heart of this innovation lies the CNC lathe factory, where precision meets automation to create parts and components that drive various industries. Understanding the intricacies of a CNC lathe factory is essential for anyone interested in metal fabrication, whether you're a business owner, engineer, or an enthusiast in the manufacturing sector.
The Evolution of CNC Technology
The evolution of CNC technology can be traced back to the late 1940s and early 1950s when the first CNC machines were developed. Today, CNC lathes have become indispensable in manufacturing, capable of producing intricate parts with unparalleled accuracy. The transition from manual machining to CNC operations has revolutionized the way components are fabricated, allowing for:
- Higher Precision: CNC lathes can achieve tolerances as tight as 0.0001 inches, making them ideal for applications requiring extreme accuracy.
- Increased Efficiency: Automation allows for continuous operation without the fatigue or errors associated with manual labor.
- Complex Geometries: CNC programming enables the production of complex shapes and designs that were previously difficult or impossible to manufacture.
These advancements highlight the necessity of a well-equipped cnc lathe factory in modern metal fabrication.
Understanding CNC Lathe Factories
A CNC lathe factory encompasses a variety of machines and processes that contribute to the production of high-quality metal parts. Let’s delve into what makes these factories so vital to the manufacturing sector.
Core Components of a CNC Lathe Factory
At the heart of a CNC lathe factory lies its essential components:
- CNC Lathes: The primary machines used for turning operations, capable of molding cylindrical parts from a variety of metals.
- Programming Software: Advanced software allows engineers to create precise instructions for the CNC lathes, controlling every aspect of the manufacturing process.
- Inspection Equipment: Quality control is crucial, utilizing tools like laser measurement systems and coordinate measuring machines (CMM) to ensure components meet specifications.
- Material Handling Systems: Efficient transportation of raw materials to and from the CNC lathes is essential for maintaining workflow.
The CNC Machining Process
The machining process in a CNC lathe factory involves several steps, all aimed at transforming raw material into a finished product:
- Design Creation: Engineers use CAD (Computer-Aided Design) software to create a digital model of the part.
- Programming: The CAD model is translated into G-code, a programming language that tells the CNC lathe how to move and operate.
- Material Preparation: Raw materials, often in the form of bars or billets, are prepared and loaded onto the machine.
- Machining: The CNC lathe performs the required operations, which can include cutting, facing, and drilling, to create the part.
- Quality Assurance: Finished parts are inspected for quality and accuracy before being shipped out.
Industry Applications of CNC Lathe Factories
CNC lathe factories cater to a wide range of industries, each with its unique requirements and specifications. Here are some prominent sectors that rely heavily on CNC machining:
- Aerospace: Precision components for aircraft and spacecraft that must adhere to strict safety regulations.
- Automotive: Production of intricate parts like engine components, transmission housings, and brake calipers.
- Medical: Manufacturing surgical instruments and devices that require impeccable precision.
- Electronics: Creation of housings and connectors that need high-performance materials and meticulous specifications.
This versatility is one of the most attractive aspects of operating within a CNC lathe factory environment.
Advantages of Working with a CNC Lathe Factory
Choosing a cnc lathe factory for your production needs offers numerous benefits:
Cost Efficiency
While the initial investment in CNC machinery can be significant, the long-term savings are undeniable. CNC lathes reduce material waste, minimize labor costs, and enhance production speed, leading to lower overall manufacturing expenses.
Scalability
Whether you need one component or thousands, CNC lathe factories can easily scale production to meet demand. This flexibility is invaluable in today’s fast-paced market.
Consistency and Quality
With CNC technology, every part produced is virtually identical. This consistency ensures that products meet stringent quality standards, reducing the risk of defects and returns.
Choosing the Right CNC Lathe Factory
When selecting a CNC lathe factory to partner with, consider the following factors:
- Experience and Expertise: Look for a factory with a proven track record in your industry.
- Technology and Equipment: Ensure they utilize the latest CNC machinery and software.
- Quality Control Measures: Investigate their approaches to quality assurance and testing.
- Customer Support: Reliable communication and support can make a significant difference in your experience.
The Future of CNC Lathe Factories
As technology continues to advance, the future of CNC lathe factories looks promising. Innovations such as artificial intelligence, machine learning, and the Internet of Things (IoT) are set to enhance operational efficiency further. Factories that adapt to these technologies will lead the industry by:
- Optimizing Production Processes: AI can predict maintenance needs, reducing downtime.
- Enhancing Customization: Advanced software will allow for greater customization of parts on a larger scale.
- Improving Supply Chain Management: Real-time data sharing can streamline supply chains and reduce lead times.
Conclusion
In conclusion, the CNC lathe factory plays a vital role in modern manufacturing, providing precision and efficiency that are essential to countless industries. As technology evolves, these factories will continue to push the boundaries of what is possible in metal fabrication. For businesses seeking to remain competitive, partnering with a reputable CNC lathe factory is more than just a choice; it's a necessity for success.
Understanding the capabilities and advantages of CNC lathe factories empowers businesses to make informed decisions that can significantly impact their operational efficiency and product quality. As the industry moves towards a more technologically advanced future, staying informed and adaptive will be key in reaping the benefits of this vital manufacturing technology.